Unveiling the Power of Titanium in Modern Manufacturing: The Definitive Guide to Titanium Fasteners and Titanium Standard Parts Manufacturers
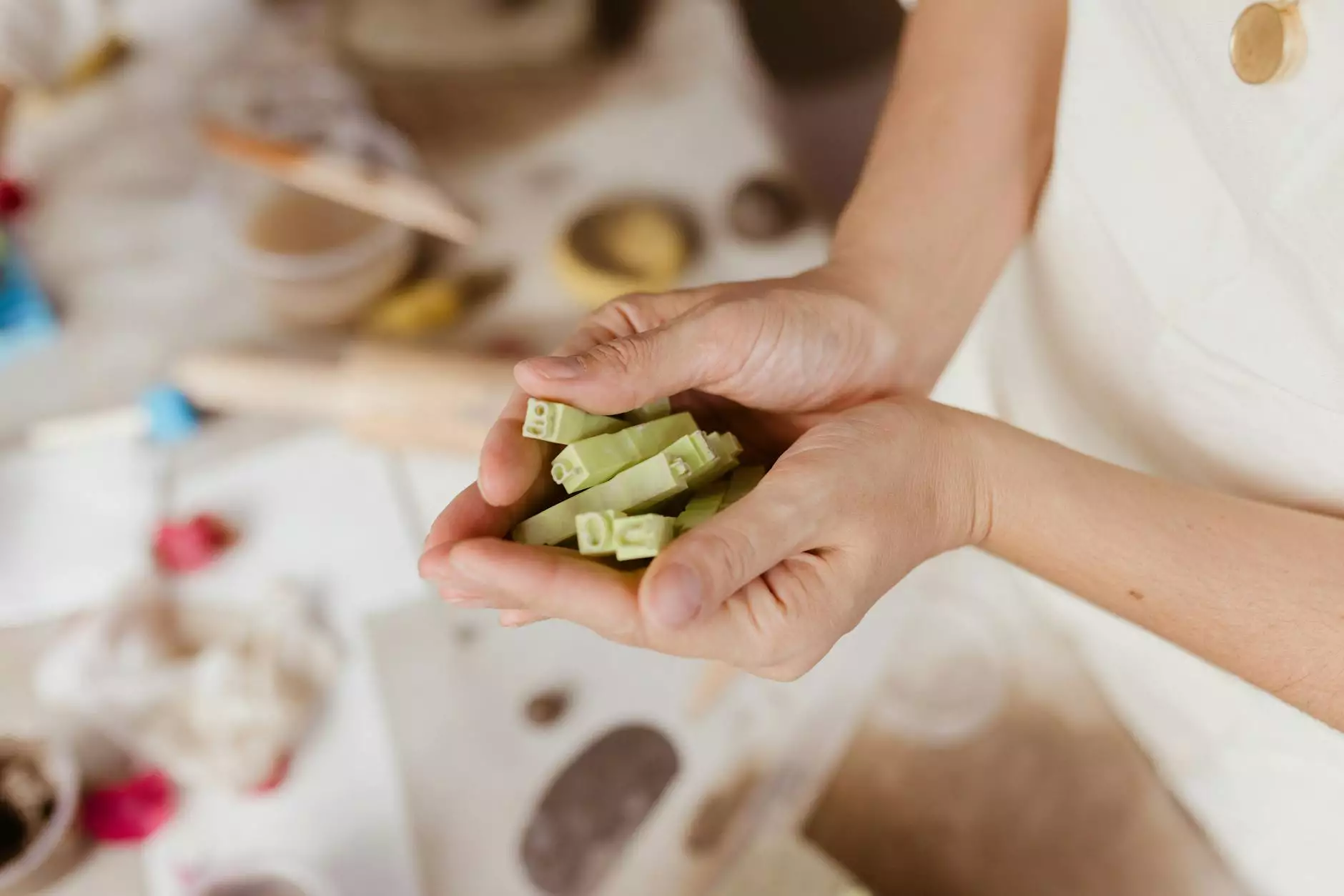
In today's rapidly evolving industrial landscape, the demand for high-performance, durable, and corrosion-resistant materials has never been greater. Among these materials, titanium stands out as an exceptional choice, revolutionizing industries such as aerospace, automotive, medical, marine, and construction. As a premier titanium fasteners manufacturer, titaniumbolts.com is committed to delivering top-tier titanium standard parts that meet the highest standards of quality and performance. This comprehensive guide explores the significance of titanium fasteners, the role of expert titanium standard parts manufacturers, and why choosing the right supplier can elevate your project's success.
The Growing Importance of Titanium in Modern Industry
Titanium's unique combination of properties makes it an ideal material for manufacturing fasteners that require resilience under extreme conditions. Its exceptional strength-to-weight ratio ensures structural integrity without adding unnecessary weight, a critical factor in aerospace and automotive applications. Additionally, titanium exhibits superior corrosion resistance, particularly in marine environments and chemical processing, significantly extending the lifespan of fasteners exposed to harsh conditions.
As industries expand their reliance on sophisticated materials, the need for reliable titanium standard parts manufacturers increases correspondingly. The capability to produce consistent, high-quality fasteners in large volumes—while maintaining stringent standards—embodies the core of successful titanium fastening solutions.
Why Choose Titanium Fasteners?
The decision to utilize titanium fasteners is driven by several compelling advantages:
- Corrosion Resistance: Titanium resists oxidation and corrosion, especially in saltwater and acidic environments, reducing maintenance costs and increasing durability.
- High Strength-to-Weight Ratio: Achieves remarkable strength while remaining lightweight, ideal for aerospace and automotive industries seeking performance without weight penalty.
- Biocompatibility: Perfect for medical implants and devices, titanium is biocompatible, minimizing adverse reactions.
- Temperature Resistance: Withstands high temperatures, ensuring stability in demanding environments such as jet engines and chemical reactors.
- Longevity and Reliability: Longer service life compared to traditional materials, providing cost savings over time.
The Role of Titanium Standard Parts Manufacturers in Industry Excellence
Titanium standard parts manufacturers play a pivotal role in the supply chain by ensuring that fasteners meet exact specifications, safety standards, and quality benchmarks. They are responsible for:
- Material Selection and Testing: Sourcing premium-grade titanium billets and conducting rigorous testing to certify material purity and mechanical properties.
- Precision Manufacturing: Employing advanced CNC machining, heat treatment, and surface finishing techniques to produce fasteners with perfect dimensions and surface quality.
- Quality Control: Implementing comprehensive inspections — including dimensional checks, tensile testing, and corrosion assessments — to ensure compliance with industry standards.
- Customization and Innovation: Offering tailored solutions for specific industries, such as aerospace-grade fasteners, medical implant screws, or marine bolts.
Partnering with a reputable titanium standard parts manufacturer guarantees not only product quality but also supplier reliability, timely delivery, and flexible order quantities—crucial factors for project success.
Industries Transformed by Titanium Fasteners
The versatility of titanium fasteners extends across many sectors. Here’s an in-depth look at how they revolutionize various industries:
Aerospace
In aerospace applications, every gram counts. Titanium fasteners are indispensable for their superb strength and weight-saving properties. They are used extensively in aircraft fuselage, engine components, and satellite modules to enhance fuel efficiency and structural safety.
Automotive
High-performance vehicles and electric cars benefit from titanium fasteners due to their durability and weight reduction capabilities. They improve handling, fuel economy, and crashworthiness, especially in racing and luxury segments.
Medical and Dental
Titanium's biocompatibility makes it ideal for surgical screws, implants, and prosthetics. Titanium standard parts manufacturers ensure that these fasteners adhere to sterilization standards, possess precise dimensions, and offer long-term stability inside the human body.
Marine & Offshore
Marine fasteners endure constant exposure to saltwater and variable weather conditions. Titanium's corrosion resistance drastically extends service life, reducing maintenance costs and enhancing safety in ships, submarines, and offshore platforms.
Construction & Infrastructure
For critical structural applications requiring longevity and resilience, titanium fasteners provide an excellent solution. They are used in bridges, architectural cladding, and environmental structures exposed to aggressive environments.
How to Choose the Best Titanium Standard Parts Manufacturers
Selecting the right manufacturer is an essential step toward ensuring your project's success. Here are key factors to consider:
- Certification & Standards Compliance: Ensure that the manufacturer complies with ISO, ASTM, or equivalent standards for titanium fasteners.
- Material Quality: Verify the source of titanium billets and confirm testing reports for chemical composition and mechanical properties.
- Manufacturing Capabilities: Look for advanced machinery, in-house testing facilities, and the ability to produce custom fasteners.
- Quality Assurance Processes: Check for rigorous inspection routines and traceability systems.
- Experience & Reputation: Choose established manufacturers with proven track records in your industry.
- Customer Support & Lead Times: Ensure responsive communication, technical support, and reliable delivery schedules.
Innovations and Future Trends in Titanium Fastener Manufacturing
As technology advances, titanium standard parts manufacturers are adopting innovative processes:
- additive manufacturing (3D printing): Enables complex geometries, rapid prototyping, and on-demand production.
- Surface Treatments: Advanced coatings and surface modifications improve wear resistance and reduce friction.
- Automation & Digitalization: Integrating Industry 4.0 technologies enhances precision, efficiency, and traceability.
- Sustainable Practices: Eco-friendly sourcing and manufacturing processes are becoming standard, reducing environmental impact.
Conclusion: The Strategic Edge of Choosing Quality Titanium Fasteners
In summary, the importance of selecting a reputable titanium fasteners manufacturer cannot be overstated. High-quality titanium standard parts translate into safer, longer-lasting, and more efficient products across a multitude of industries. With breakthroughs in manufacturing technology and stringent quality controls, the future of titanium fasteners looks promising, offering unmatched performance and sustainability.
For businesses seeking to elevate their engineering standards and operational efficiency, partnering with industry-leading manufacturers like titaniumbolts.com provides a compelling advantage. As a trusted titanium fasteners manufacturer, our commitment is to supply superior fasteners that meet your project's precise requirements—driving innovation, safety, and success in your industry.