The Ultimate Guide to Mould Manufacturers: Transforming Industries with Precision Engineering
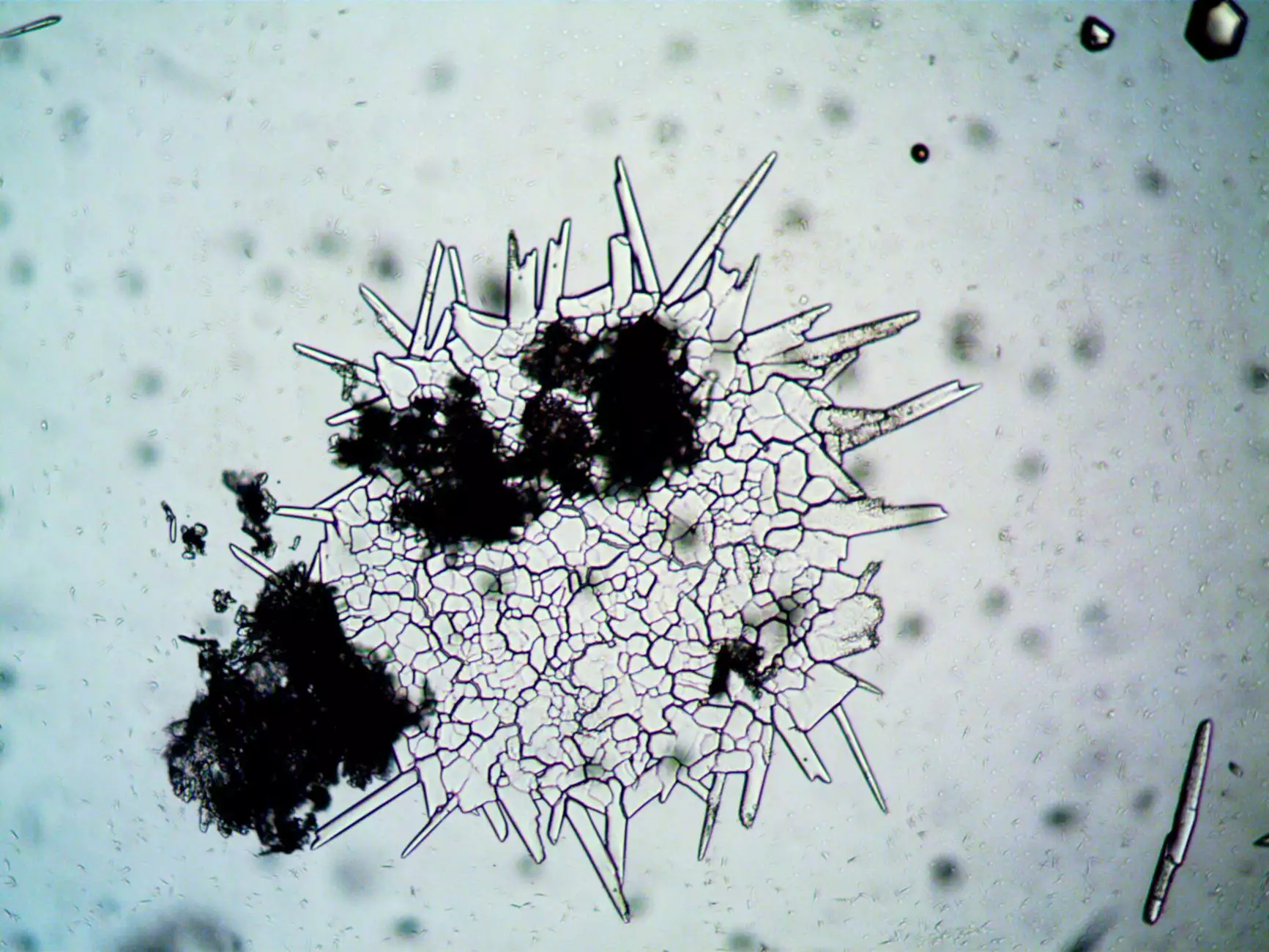
In today’s rapidly evolving industrial landscape, the role of mould manufacturers has become increasingly pivotal. They are the backbone of modern manufacturing, supplying critical components that allow for the efficient production of a myriad of products ranging from automotive parts to consumer goods. Understanding the intricacies of the mould manufacturing process not only reveals the technical expertise involved but also highlights the competitive edge businesses can gain through collaboration with top-tier manufacturers like Hanking Mould.
What Are Moulds and Why Are They Important?
Moulds are hollow forms used to give shape to molten or hot liquid material. The material is poured into the mould and cooled to form a solid object. Typically, moulds are made from metals such as steel, aluminum, or brass, which can withstand high temperatures during the manufacturing process. The significance of moulds is paramount for several reasons:
- Efficiency: Moulds enable mass production by streamlining the manufacturing process, thereby reducing labor costs and time.
- Precision: High-quality moulds produce precise components, ensuring consistency across multiple units.
- Cost-Effectiveness: Although initial investment in moulds can be high, they significantly reduce costs over time by allowing for quicker production rates.
- Material Versatility: Moulds can be designed for a variety of materials including plastics, metals, and other composites.
The Role of Plastic Mold Makers
Plastic mold makers specialize in creating moulds that are used specifically for plastics. This area of expertise is crucial for industries such as automotive, consumer electronics, and packaging. The process typically involves several key stages:
1. Design and Engineering
The initial step involves creating a design that meets the specifications of the final product. Advanced software tools like CAD (Computer-Aided Design) are utilized to visualize and refine the design before moving forward. This phase is critical, as any errors here can lead to costly revisions later.
2. Material Selection
Choosing the right material for the mould is essential. Factors such as durability, heat resistance, and tolerance levels must be considered. For plastic applications, steel or aluminum are commonly used because of their ability to withstand repeated use.
3. Machining and Fabrication
Once the design is finalized and materials selected, the fabrication process begins. This involves machining the mould using precision equipment like CNC machines to ensure exact specifications are met. The entire process is meticulously monitored to maintain quality standards.
4. Testing and Quality Assurance
Before production can commence, the mould undergoes rigorous testing. This ensures that it operates effectively and produces parts that meet the necessary quality standards. Any necessary adjustments are made to optimize performance.
Exploring Plastic Injection Mould Manufacturers
Plastic injection mould manufacturers take the engineering prowess of plastic mold makers a step further by specializing in the injection molding process—a method that involves injecting molten plastic into a mould cavity. This method is particularly popular due to its ability to produce complex and intricate designs efficiently. Here’s how it works:
1. Injection Process
The injection molding process begins with heating plastic pellets until they melt. This molten plastic is then injected into the mold under high pressure, allowing it to fill every cavity. This method is favored for its speed and efficiency, with cycles often taking mere seconds.
2. Cooling and Solidification
Once the molten plastic is injected, it cools and solidifies to take on the shape of the mould. The cooling time is a crucial factor that can impact production rates. Advanced manufacturers utilize techniques like water cooling to streamline this process.
3. Ejection and Finishing
After the plastic has cooled and solidified, ejector pins are used to remove the finished part from the mould. Additional finishing processes such as trimming, sanding, or painting may be applied to enhance the appearance and functionality of the final product.
Why Choose Hanking Mould for Your Mould Manufacturing Needs
Hanking Mould stands out as a premier choice among mould manufacturers for the following reasons:
1. Expertise and Experience
With years of experience in the field, Hanking Mould has honed its techniques and processes to deliver moulds that meet the highest standards of quality and precision. Their team of skilled engineers is adept at translating complex designs into functional moulds.
2. Advanced Technology
Hanking Mould employs cutting-edge technology to enhance the manufacturing process. This includes advanced machinery and software that improve design accuracy and production efficiency.
3. Customer-Centric Approach
The company places a strong emphasis on customer satisfaction. They work closely with clients to understand their unique needs and provide tailored solutions. This collaborative approach helps ensure that the final product aligns with the client’s vision and requirements.
4. Commitment to Quality
Quality assurance is at the forefront of Hanking Mould’s manufacturing process. Every mould produced undergoes exhaustive testing to ensure it meets stringent quality standards before it reaches the client.
Future Trends in Mould Manufacturing
As industries continue to evolve, mould manufacturers must stay ahead of the curve. Here are some trends shaping the future of the mould manufacturing industry:
- 3D Printing Technologies: The rise of 3D printing is revolutionizing how moulds are designed and produced, allowing for faster prototyping and reduced material waste.
- Sustainability: Increasing demand for sustainable practices is prompting manufacturers to explore eco-friendly materials and processes.
- Automation: The integration of automation and Industry 4.0 technologies is enhancing efficiency and precision in the mould manufacturing process.
- Customized Solutions: As businesses seek unique products, there is a growing trend towards customized mould solutions tailored to specific applications.
Conclusion
In conclusion, mould manufacturers play a vital role in the industrial fabric of our society, enabling businesses to produce high-quality products with efficiency and precision. With experts like Hanking Mould at the helm, the future looks promising for mould manufacturing. By embracing new technologies and maintaining a focus on quality and customer satisfaction, mould manufacturers will continue to thrive and adapt to the changing needs of the market.
A collaboration with reliable manufacturers ensures that businesses are equipped with the best tools and resources to meet their production demands. For businesses looking to invest in high-quality moulds tailored to their needs, partnering with a reputable supplier like Hanking Mould is essential for success.