CNC Machining Factory: Revolutionizing Manufacturing with Precision and Efficiency
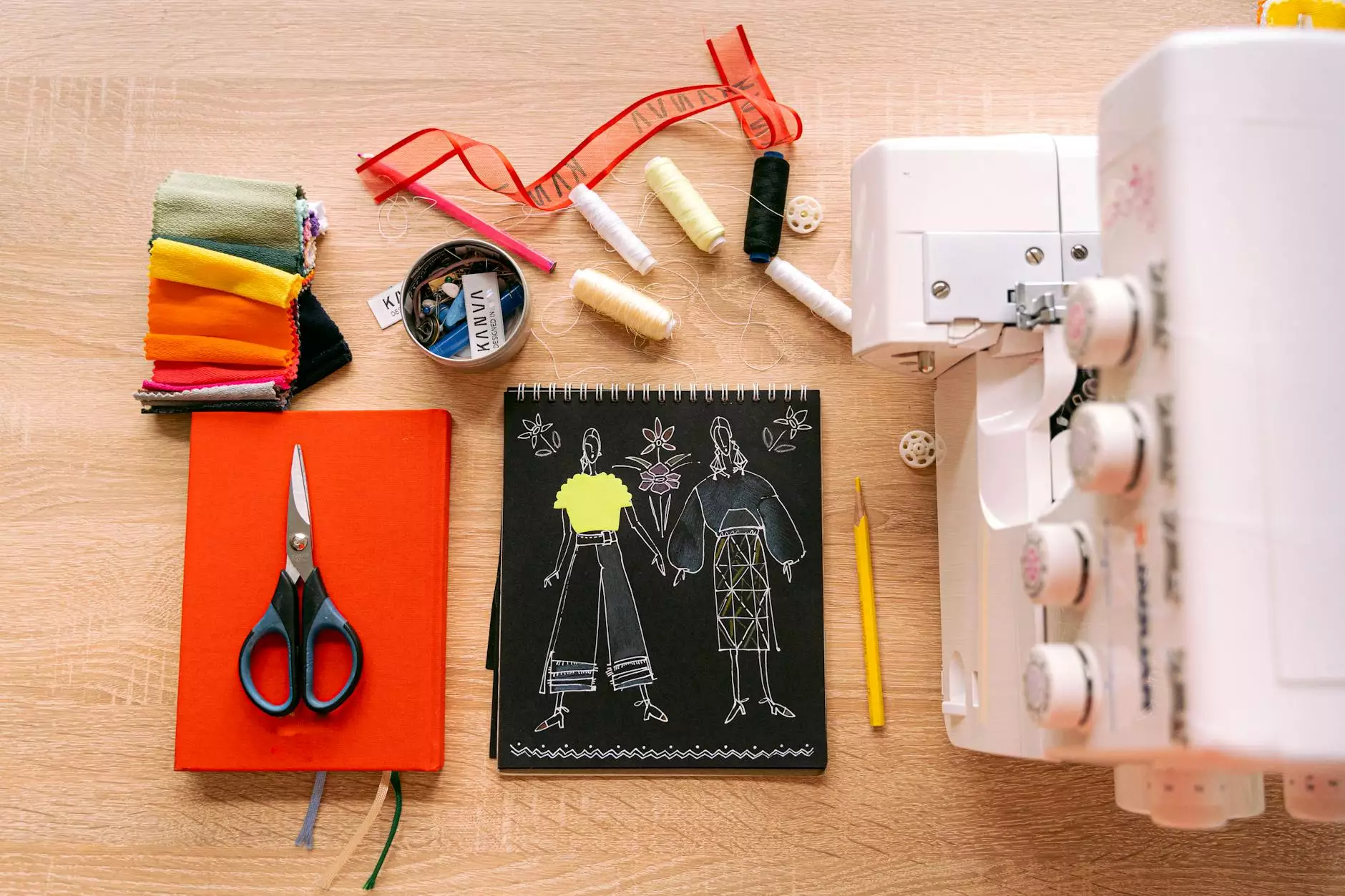
In the competitive landscape of modern manufacturing, cnc machining factories stand out as a beacon of innovation and efficiency. These facilities harness the power of advanced technology to produce high-quality parts and components with unparalleled precision. Whether you are in the automotive, aerospace, medical, or consumer goods sector, understanding the capabilities and advantages of CNC machining can significantly impact your business's success.
What is CNC Machining?
CNC, or Computer Numerical Control, is a process that involves the use of computers to control machine tools. This technology allows for the automation of complex machining operations, where precision and consistency are paramount. CNC machining can be utilized for various materials, including metals, plastics, and composites, and is fundamental to the operations of a cnc machining factory.
Types of CNC Machining Processes
- Milling: This involves cutting material using rotating multi-point cutting tools. It's ideal for producing complex shapes and features.
- Turning: In this process, a cutting tool takes material from a rotating workpiece. It’s commonly used for creating cylindrical parts.
- Drilling: Drilling machines create holes in various materials with precision and accuracy.
- EDM (Electrical Discharge Machining): This technique uses electrical discharges to remove material. It's particularly useful for hard metals.
- Laser Cutting: A focused laser beam cuts through materials, enabling intricate designs and high-speed processing.
The Importance of Precision in CNC Machining
Precision is a cornerstone of manufacturing excellence, and cnc machining factories offer several advantages in this regard:
1. Enhanced Accuracy
CNC machines are designed to deliver tight tolerances, often within plus or minus 0.001 inches. This reliability means that components fit together seamlessly, which is essential in applications ranging from aerospace to medical devices.
2. Consistency in Production
Once a CNC program is set up, it can replicate the design repeatedly without variation. This consistency is vital for industries requiring large volumes of identical parts.
3. Complex Geometries Made Simple
With CNC machining, manufacturers can produce intricate designs that would be impossible to achieve with traditional methods. This capability allows for product innovation and differentiation in competitive markets.
Cost Efficiency in CNC Machining
While the initial setup for CNC machining can be significant, the long-term cost savings are significant. Here's how:
1. Reduced Labor Costs
The automation of machining processes means that fewer operators are needed on the shop floor. Operators can oversee multiple machines, reducing labor costs and increasing productivity.
2. Minimal Material Waste
CNC machining optimally utilizes materials, significantly reducing waste associated with manual machining techniques. This efficiency translates to savings on raw material costs.
3. Faster Production Times
The speed of CNC machines means that production cycles are shorter. Rapid prototyping and production enable businesses to respond quickly to market demands.
Technological Advancements in CNC Machining
The world of CNC machining is ever-evolving, with technological advancements continually enhancing capabilities. Here are some significant trends:
1. Integration with IoT (Internet of Things)
Many modern CNC machines are IoT-enabled, allowing for real-time monitoring of machine performance and maintenance needs. This connectivity enhances operational efficiency.
2. Additive Manufacturing Synergy
CNC machining is increasingly being combined with additive manufacturing technologies. This synergy allows for creating complex geometries with a blend of subtractive and additive techniques.
3. Artificial Intelligence in CNC Operations
AI is making its way into CNC machining for predictive maintenance, quality control, and optimizing machining parameters. This integration is driving the future of intelligent manufacturing.
Quality Control in CNC Machining
Ensuring quality in a cnc machining factory is essential to maintain standards and customer satisfaction. The following methods are utilized:
1. In-Process Inspection
During manufacturing, machines can be equipped with sensors that measure tolerances live, allowing for immediate adjustments to maintain quality.
2. Final Product Testing
Products are often subjected to rigorous testing after machining to ensure they meet specification requirements. This may include physical measurements, stress tests, and visual inspections.
3. Certification and Compliance
Many CNC machining factories comply with international standards such as ISO 9001, ensuring that their processes and products meet high-quality benchmarks.
The Role of CNC Machining in Various Industries
CNC machining plays a crucial role in diverse industries, enhancing production capabilities and innovation:
1. Aerospace Industry
The aerospace sector demands high precision and reliability in all components due to safety concerns. CNC machining allows for the production of complex aircraft parts that meet stringent industry standards.
2. Automotive Industry
The automotive industry benefits from CNC machining's ability to produce durable and precise components required for modern vehicles' efficiency and safety.
3. Medical Industry
In the medical field, precision is life-critical. CNC machining produces surgical instruments and implants with tight tolerances that ensure patient safety and effectiveness.
4. Consumer Products
CNC machining is instrumental in creating high-quality consumer products, from electronics to appliances, providing design flexibility and customization options.
Challenges Facing CNC Machining Factories
Despite their advantages, CNC machining factories face several challenges:
1. High Initial Investment
The cost of CNC machines and the necessary software can be hefty. Small or startup manufacturers may find it challenging to invest in this technology.
2. Skilled Labor Shortage
Advanced CNC machines require skilled operators, and many industries are facing a shortage of workers trained in these technologies.
3. Keeping Up with Technological Changes
The rapid pace of technological advancements can create pressure on factories to continually upgrade their machines and software, adding to operational costs.
Conclusion: The Future of CNC Machining
The future of cnc machining factories is bright as they adapt to the changing landscape of manufacturing. With ongoing investments in technology and workforce training, these facilities will continue to lead the charge in producing high-quality components efficiently. The advantages of precision, cost efficiency, and technology integration position CNC machining as a vital part of modern manufacturing processes.
As industries continue to evolve, the essential role of CNC machining will remain, driving innovation, efficiency, and sustainability in manufacturing. Companies looking to stay competitive must consider the immense benefits that partnering with a reputable CNC machining factory, such as Deep Mould, can offer.